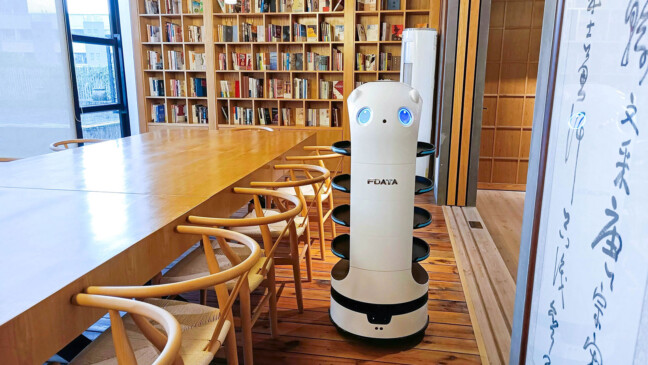
03.04.23
Sur le marché pharmaceutique, il existe une large gamme de solutions de traitement pour le nettoyage et la passivation des installations pharmaceutiques en acier inoxydable. Leur développement dans le but d'obtenir des améliorations économiques et écologiques s'est fait principalement en modifiant progressivement les compositions chimiques des solutions de traitement.
Un film passif intact est indispensable pour la résistance à la corrosion des installations pharmaceutiques. La résistance à la corrosion n’est toutefois pas une propriété du matériau, mais dépend du matériau et de l’environnement du système de corrosion concerné. Les systèmes de corrosion dans cet environnement (installations pharmaceutiques en acier inoxydable) sont généralement de nature électrochimique. Il ressort des lois de cette nature électrochimique que, dans un système de corrosion existant, la corrosion caverneuse est toujours la première forme de corrosion à apparaître. Ces connaissances confirment l’expérience existante selon laquelle, pour ce groupe de matériaux, tout ce qui n’est pas un film passif intact peut constituer une fissure. Il en résulte que: Le nettoyage, c’est-à-dire l’élimination de ces fentes potentielles, revêt une importance décisive pour qu’un film passif efficace puisse se former. Il est donc logique d’utiliser des méthodes d’analyse électrochimique pour classifier et optimiser les solutions de passivation.
Il existe sur le marché pharmaceutique une large gamme de solutions de traitement pour le nettoyage et la passivation des installations pharmaceutiques en acier inoxydable. Leur développement dans le but d’obtenir des améliorations économiques et écologiques s’est fait principalement en modifiant progressivement les compositions chimiques des solutions de traitement. Il est bien connu que dans ce groupe de matériaux, c’est surtout la qualité du film passif qui détermine si les influences négatives du milieu environnant sont limitées. Il est donc logique d’examiner de plus près la surface du matériau en contact avec le produit, car c’est seulement dans cette zone de contact – également appelée limite de phase – entre le matériau et le milieu que des influences réciproques peuvent se produire.
En traitement de surface, la passivation désigne l’apparition spontanée ou la production ciblée d’un film protecteur qui empêche pratiquement la corrosion du matériau métallique. L’une des significations techniques les plus connues de ce phénomène est l’utilisation d’aciers inoxydables CrNi(Mo), qui sont principalement utilisés dans les installations de l’industrie chimique et pharmaceutique. La cause de cette passivité est l’élément d’alliage chrome, qui doit être contenu dans l’acier inoxydable dans une proportion d’au moins 13% en masse pour qu’un film passif correspondant puisse se former à la surface. Ce film passif se forme spontanément dans l’environnement naturel (d’où les aciers inoxydables) et est en équilibre thermodynamique avec lui. Par conséquent, un film passif peut se dégrader dans un autre environnement au point de provoquer des phénomènes de corrosion. Mais d’un autre côté, il peut aussi être optimisé par un traitement défini de sorte qu’il constitue la protection efficace contre la corrosion qui lui est destinée. L’expérience montre également que des types de corrosion locale peuvent être initiés, en particulier aux points faibles et perturbateurs du film passif, ce qui, dans le cas des aciers inoxydables, est étroitement lié à la présence d’ions chlorure.
Plus précisément, les aciers inoxydables sont uniquement des aciers qui ne forment pas de rouille dans l’air humide ou dans l’eau sans conditions limites aggravant la corrosion. Selon la composition du matériau, des conditions plus agressives sont également tolérées. Cette restriction conduit à la définition de la corrosion dans la norme DIN EN ISO 8044 : “La corrosion est l’interaction physico-chimique entre un métal et son environnement, qui entraîne une modification des propriétés et qui peut avoir des répercussions importantes sur le fonctionnement du métal, de l’environnement ou du système technique dont ils font partie. Cette interaction métal/environnement est souvent de nature électrochimique”. En résumé, la résistance à la corrosion n’est donc pas une propriété du matériau, mais une propriété du système.
Ce mécanisme se caractérise par le fait que l’attaque de corrosion se produit exclusivement à la limite de phase entre un conducteur d’électrons (métal) et un conducteur d’ions (électrolyte comme environnement). La corrosion électrochimique est une réaction d’oxydoréduction dont la réaction totale peut toujours être décrite en 2 réactions partielles. La réaction partielle anodique est, en tant que processus de dissolution du métal, la réaction de corrosion proprement dite. Cette réaction correspond à un processus d’oxydation au cours duquel des électrons sont produits à l’anode. Pour des raisons d’électroneutralité, cette réaction qui fournit des électrons doit s’opposer à une réaction qui en consomme à la cathode. La réaction cathodique partielle correspondant à un processus de réduction commande le processus de corrosion correspondant. Les deux réactions partielles se déroulent alors simultanément à la surface du métal (avec le même taux de conversion des électrons, mais pas au même endroit) et conduisent à une séparation des charges grâce à leur taux de conversion des charges. Cette séparation de charge peut être mesurée par rapport à une référence définie sous forme de potentiel.
En raison de la nature électrochimique des processus de corrosion considérés ici, les études électrochimiques constituent un élément important de la recherche sur la corrosion. Parmi les nombreuses méthodes, l’enregistrement des courbes densité de courant-potentiel dans le milieu d’attaque respectif s’est avéré particulièrement pertinent pour les aciers inoxydables. Il est également possible de déduire des relations fondamentales à partir du tracé de la courbe. Pour déterminer les courbes densité de courant/potentiel, la densité de courant (courant par surface) est analysée dans un électrolyte à l’aide d’un circuit électrique spécial comme mesure de la vitesse de corrosion en fonction d’un potentiel modifié de manière dynamique et ciblée. La plupart du temps, on enregistre les courbes de tension de courant et on en déduit la densité de courant ainsi que le potentiel avec la référence correspondante. Pour les aciers inoxydables, on obtient des courbes caractéristiques et en principe identiques dans de nombreux électrolytes neutres et légèrement acides (figure 1). Pour l’utilisation des aciers inoxydables, cela signifie que le choix du matériau doit d’abord être fait de manière à ce que le système composé du matériau et du milieu environnant se trouve dans une zone passive stable dans les conditions données (figure 2). Par conséquent, les matériaux qui présentent la plus grande résistance à la corrosion sont ceux qui possèdent la plus large plage passive dans le milieu concerné. D’autre part, ce comportement de principe dans le domaine passif démontre également la sensibilité aux perturbations du système. D’une part, des modifications du milieu ou de petites modifications des conditions physiques et chimiques dans le milieu peuvent entraîner une modification négative de l’allure de la courbe (par ex. une plage passive plus étroite). D’autre part, des points faibles et perturbateurs dans le film passif peuvent initier des types de corrosion locaux (par ex. la corrosion par piqûres, lorsque, en présence d’ions chlorure, le potentiel de repos commun Ecorr est plus positif que le potentiel de dépassivation Ed ; voir également la figure 2). Une autre méthode d’analyse électrochimique dynamique, dans laquelle le potentiel est inversé lorsqu’un courant défini est atteint, apporte des informations supplémentaires sur la stabilité de la zone de passivation (figure 3). Il ressort de cette courbe que la corrosion par fissure et la corrosion par piqûre sont toutes deux des types de corrosion dépendant du potentiel, qui apparaissent au-dessus de potentiels critiques spécifiques. La principale conclusion est que, pour un même système de corrosion, le potentiel au-dessus duquel la corrosion caverneuse se produit est toujours plus négatif que le potentiel comparable au-dessus duquel la corrosion par piqûres se produit. Par conséquent, la corrosion caverneuse est le type de corrosion qui apparaîtrait toujours en premier dans un système de corrosion potentiellement existant. Dans un système de corrosion donné, le risque lié à la corrosion caverneuse est donc toujours plus important que celui lié à la corrosion par piqûres.
Pour la sécurité des installations dans l’industrie chimique et pharmaceutique, les connaissances citées jusqu’ici signifient que la résistance à la corrosion des aciers inoxydables principalement utilisés ici dépend avant tout d’un film passif intact. Il est bien connu que des impuretés de toutes sortes dans la zone de la surface rendent difficile la formation ou le maintien d’un film passif intact et peuvent conduire à un point faible ou à un point de défaillance. Les points faibles ou perturbateurs dans le film passif sont prédéterminés en tant qu’anodes potentielles (lieu de dissolution du métal = corrosion) dans le système de corrosion latent existant. Il importe peu que ces points faibles ou perturbateurs soient déjà introduits lors de la transformation des matériaux et/ou pendant le fonctionnement de l’installation. Les impuretés typiques lors de la fabrication sont les couleurs de revenu, les résidus de graisse et d’huile, la calamine, les projections de meulage et de soudage, les copeaux, les poussières, les rayures. Pendant le fonctionnement, on observe principalement des dépôts et des modifications thermiques de la surface métallique ainsi que des blessures mécaniques. L’expérience montre également qu’il n’est pas possible d’éviter totalement les impuretés de toutes sortes lors de la construction et de l’exploitation d’installations techniques, c’est pourquoi une solution de passivation ne doit pas seulement soutenir et accélérer le mécanisme de passivation naturel existant de toute façon, mais aussi présenter un pouvoir nettoyant élevé contre les impuretés préjudiciables. Par conséquent, une solution de passivation – même si elle contient beaucoup de composants oxydants – ne peut pas déployer son effet si elle n’est pas capable d’éliminer les impuretés présentes et donc de rendre la surface métallique accessible.
Donnez-nous votre avis
Ecrire le premier commentaire sur cet article.
Sie müssen angemeldet sein, um einen Kommentar zu hinterlassen.