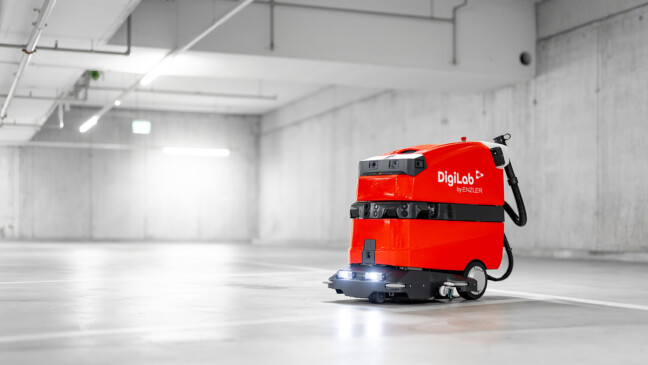
09.09.24
In today's professional world, technical specifications and precise designs play an essential role - especially in sensitive areas such as operating theaters. The following field report provides a detailed insight into the complex process of sealing the floor in the clinic on Lake Constance, in which the conductivity of the floor played a central role.
The clinic’s original operating theater floor was planned to the highest technical standards: dissipative, with copper strips under the flooring that were connected to the building’s cabling. Conductive PVC panels were laid on top, which were welded to ensure a continuous surface. Coved plinths were installed on top to comply with the operating theater specifications. So far, everything was going according to plan. However, over time, various changes and measures were made that had a lasting impact on the progress of the project. A 2-component sealant was applied, whose properties in terms of conductivity could no longer be reproduced at this point. The fact that this seal had a yellow color makes it clear that the focus here was less on technical specifications and more on aesthetic considerations. A final measurement of the discharge capacity was not carried out.
Later, another service provider stepped in and carried out a further sealing, but here too the question of conductivity remained unanswered for the time being. A later, routine check showed that the required electrical conductivity was no longer present. The clinic, which was interested in the correct functioning of the surgical floor, held talks with experts, including Peter Bischofberger from the company Atramex AG. After several consultations, it was decided to reseal the floor, this time with a product that was specified from the outset. The final choice of color was RAL5014 “Pigeon Blue” – an aesthetically pleasing choice, but again, the dissipative properties of the seal used were not initially the focus of the discussions.
One critical point was the lack of communication about the specific requirements for discharge capability. Although the product used confirmed a certain dissipative capacity, a specialized ESD seal was not offered or processed. In retrospect, the exact requirement for a special ESD seal from Atramex would have significantly changed the course of the work. When the sealing was completed and the measurements taken, it turned out that the floor once again did not meet the requirements. At this point, another technical problem was discovered: the copper strips under the floor covering were no longer connected to the house installation, which further impaired the conductivity. This damage was presumably caused by the removal of the previously installed coved plinths, which were removed and replaced with new ones every time the floor was resealed.
The solution to this problem required quick action. In close cooperation between Atramex, Enzler Reinigungen AG and the expert Mr Welter from Thurmed , an innovative solution was developed. Mr Welter suggested attaching copper strips to the existing seal and soldering them to the building installation. Only then could the final ESD seal be applied and the necessary conductivity restored. Interestingly, in retrospect it was realised that the conductivity would not have been given if the ESD seal had been applied from the outset. The floor was simply no longer able to ensure conductivity to the copper strips. This realisation shows that the problems were far deeper than originally assumed.
This experience report impressively shows how important it is to pay attention not only to the execution of technical projects, but also to the precise communication of requirements. Misunderstandings or missing information can lead to considerable challenges in later phases.
Despite all the hurdles, the collaboration between the parties involved ran smoothly and professionally. Thanks to the joint efforts, a solution was found that far exceeded the required discharge capability values. This case is an example of how complex the requirements for modern floor coverings in sensitive areas such as operating theatres are and how important it is to involve specialized products and expertise in the process. It was only through close cooperation and innovative approaches that this challenging project could be successfully completed.